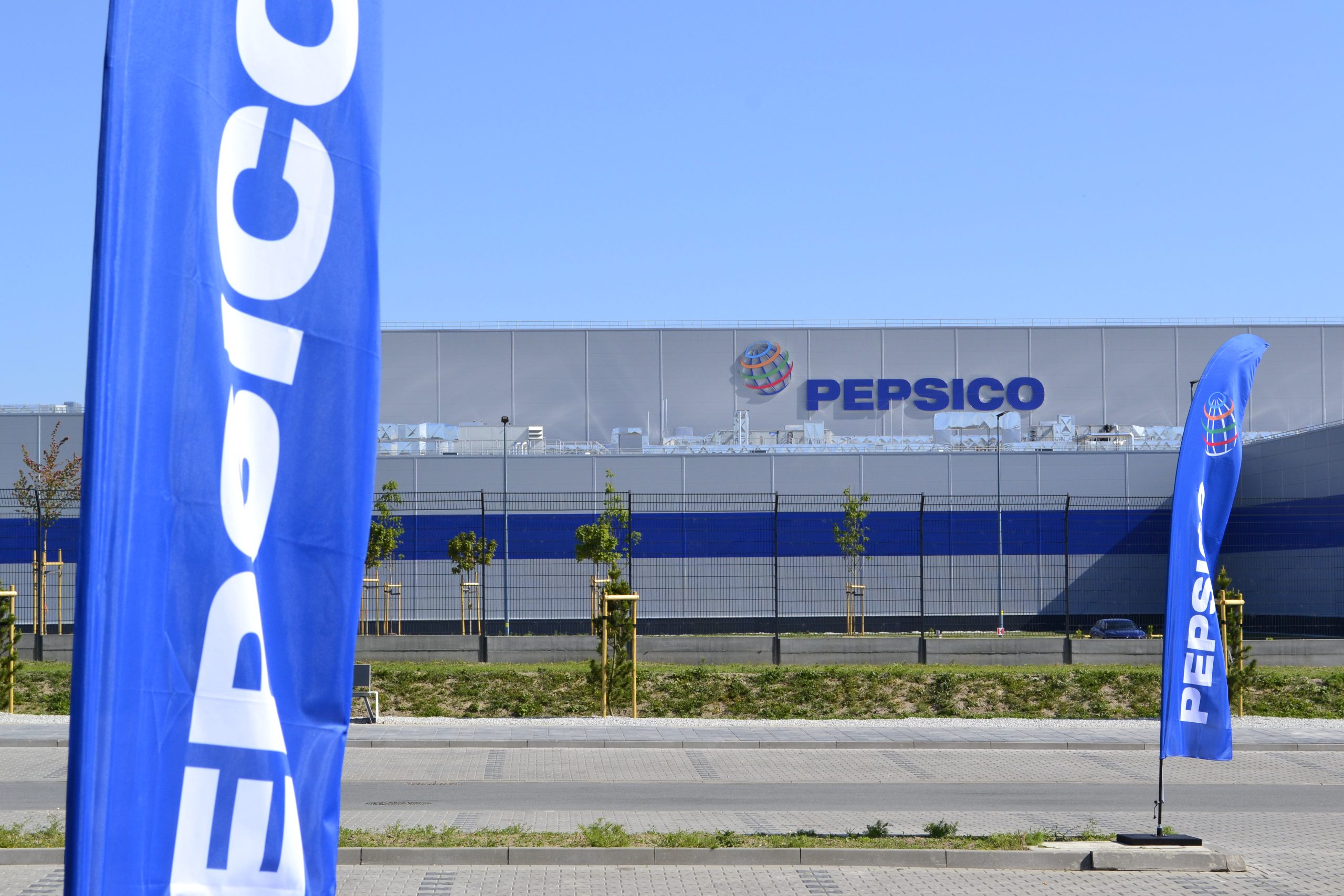
Ekologiczna fabryka znanych chipsów
Nad czym pracowało 100 ekspertów z Arup?
Piąta nieruchomość produkcyjna PepsiCo w Polsce ma dostarczać 54 tys. ton rocznie przekąsek dla marek należących do FritoLay z ziemniaków i kukurydzy. Produkty z Dolnego Śląska trafiają aż do 20 krajów świata. To najbardziej ekologiczny zakład koncernu PepsiCo w Europie. Produkuje własną energię z instalacji fotowoltaicznej, a docelowo będzie całkowicie samowystarczalna w kwestii energii elektrycznej. Nad projektem dla PepsiCo pracowało ponad 100 ekspertów z biura projektowego Arup, którzy przeanalizowali najbliższe 60 lat pod względem zeroemisyjności obiektu. Jakie konkretne rozwiązania udało się im wprowadzić i na czym polega ich innowacyjność?
PepsiCo Frito-Lay w Świętem
Fabryka Frito-Lay w miejscowości Święte koło Środy Śląskiej (woj. dolnośląskie) to najbardziej ekologiczny zakład koncernu PepsiCo w Europie. Mimo że produkcja rozpoczęła się 31 maja 2023 roku, nadal trwają prace nad rozbudową, a także wprowadzane są – według harmonogramu – kolejne zaplanowane ekologiczne rozwiązania. Planuje się, że do 2035 roku obiekt stanie się zeroemisyjny. Za realizację tego ekoprojektu odpowiedzialni są inżynierowie z firmy Arup. Generalnym wykonawcą był Budimex. Inwestycja wiąże się z powstaniem ponad 450 nowych miejsc pracy.
Obiekt produkcyjno-magazynowy z powierzchnią socjalno-biurową została zrealizowana na terenie 30,6 ha. Powierzchnia zabudowy to 54 700 m2. Sama hala produkcyjna liczy 23 000 m2. Chodniki i drogi zajęły 54 197 m2. Na całą inwestycję składa się obecnie: część produkcyjna, część socjalno-biurowa, magazynowa, a także własna oczyszczalnia wody oraz część odpowiedzialna za energię nieruchomości. Ma zostać jeszcze rozbudowywana.
Fabryka specjalizuje się w produkcji przekąsek i chipsów z ziemniaków i kukurydzy dla marek należących do FritoLay. Jest to piąta nieruchomość produkcyjna PepsiCo w Polsce. Ma dostarczać 54 tys. ton przekąsek rocznie. Produkty z Dolnego Śląska trafiają do 20 krajów świata.
Prace projektowe rozpoczęły się w kwietniu 2020 r. Za to, że jest to najbardziej ekologiczny zakład produkcyjny światowego potentata spożywczego PepsiCo, odpowiedzialny jest Arup. – Była to inwestycja typu „bid&build”, budowana praktycznie od zera – wyjaśnia Tomasz Frej, Associate w firmie inżynieryjnej Arup.
Obiekt został zaprojektowany w systemie BIM. W firmie Arup powstał cyfrowy model 3D zakładu, co ułatwiło projektowanie i zmiany w koncepcji, a w przyszłości usprawni prace serwisowe i pozwoli na ich jak najefektywniejsze procedowanie w warunkach nieprzerwanej produkcji. To rozwiązanie pozwala także na modelowanie zmian produkcji, rozbudowę podczas pracy zakładu oraz zarządzanie kosztami. Był to zarazem pierwszy model zakładu 3D dla PepsiCo w Europie.
Zmian dokonywano jeszcze na etapie tworzenia koncepcji architektonicznej. Zabudowa miała pierwotnie wynieść 30 tys. m2. Ostatecznie wybudowano 55 tys. m2. powierzchni produkcyjno-magazynowej i dodano jedną linię produkcyjną. Projekt zakłada umożliwienie łatwego rozszerzania o kolejne linie produkcyjne, bez ingerencji w istniejące już elementy i konieczności zatrzymania pracy.
– Zaprojektowaliśmy ten zakład w taki sposób, by stał się on zeroemisyjny. Przeanalizowaliśmy ślad węglowy dla 60 lat pracy zakładu – od momentu budowy, przez okres eksploatacji, po proces rozbiórki. Analiza zaczynała się już na etapie pozyskiwania materiałów. Na tej podstawie powstał projekt. Trudno jest wybudować tego typu obiekt od razu jako zeroemisyjny, więc – póki co – proces jeszcze trwa ale w ciągu kilku lat przyjęta polityka zostanie w pełni zrealizowana – opowiada Tomasz Frej, Associate, Arup. – Projekt stworzono przez naszych inżynierów, we współpracy z inżynierami procedur produkcyjnych z PepsiCo – dodaje ekspert z firmy Arup.
Inżynierowie w akcji
Nad projektem dla PepsiCo pracowało ponad 100 ekspertów z Arup. Lista ich zadań obejmowała: cały proces inwestycyjny, proces technicznego due dilligence działek, koncepcję, projekt wykonawczy, a także doradztwo środowiskowe w obszarze zrównoważonego rozwoju, geotechnikę, projekt schematu ekologii fabryki. Dodatkowo firma zrealizowała proces uzyskiwania pozwoleń, w tym środowiskowych, pozwolenia na budowę itd. Efektywnie przeprowadziła przetarg na Generalnego Wykonawcę, którym został Budimex. Do prac przy projekcie należało także: doradztwo kosztowe, zarządzanie projektem w czasie budowy, nadzór inwestorski, usługi w okresie uruchomień i odbiorów oraz nadzór autorski nad projektem, co gwarantowało zrównoważony rozwój inwestycji.
Konstrukcja ekologii
Już w trakcie budowy zastosowano liczne proekologiczne technologie. Wykorzystano m.in. materiały o niskim śladzie węglowym, zaplanowano także użycie takich materiałów, by można je było wykorzystać w przyszłości. – Konstrukcja jest stalowa. Betonowa generowałaby dużo większy ślad węglowy – wyjaśnia Tomasz Frej. W miarę możliwości w trakcie budowy położono nacisk na zamówienia materiałów od lokalnych dostawców, aby zmniejszyć emisję z transportu. Posadzka budynku biurowego została wykonana z granitu z lokalnych kopalń, co ograniczyło emisję związaną z transportem materiału.
Fabryka produkuje własną energię z instalacji fotowoltaicznej, docelowo będzie całkowicie samowystarczalna w kwestii energii elektrycznej. – Obecnie panele fotowoltaiczne są zainstalowane na hali produkcyjnej – mówi Tomasz Frej i dodaje, że pod kolejne został już przygotowany dach magazynu. Docelowo zaplanowano jeszcze własną farmę fotowoltaiczną oraz turbinę wiatrową na terenie nieruchomości. Teraz głównym źródłem ciepła do podgrzewania produktów jest gaz, ale ta instalacja zostanie zastąpiona przez podgrzewacze wykorzystujące własny zielony prąd. Natomiast woda służąca do mycia linii produkcyjnych jest podgrzewana ciepłem, które odbierane jest z systemu podgrzewania oleju do smażenia przekąsek. Ten system zaprojektował Arup razem z inżynierami z PepsiCo.
Aby uniknąć budowy magazynu w celu przechowywania ziemniaków i kukurydzy, zaplanowano szczegółowy i precyzyjny plan dostaw surowców od rolników z regionu. Krótsza droga dostaw ma wpłynąć na zmniejszenie emisji spalin.
Ciepło-zimno z odzysku
Zarówno do chłodzenia, jak i podgrzewania wody czy powietrza wykorzystuje się jedynie ciepło odpadowe, które powstaje podczas procesu produkcji przekąsek.
Część produkcyjna dzieli się na linię wytwarzania chipsów ziemniaczanych metodą smażenia, linię do wypieku produktów ziemniaczanych oraz linię wyrobów z kukurydzy. – Maszyny produkcyjne wymagają dużo energii, pracują z wysokimi temperaturami. Przez to warunki na halach są dość trudne – pod sufitem temperatura sięga 60 stopni Celsjusza – dlatego uporanie się i odzysk tego ciepła odgrywał ważną rolę. To ciepło jest m.in. używane do produkcji chłodu, a także podgrzewania wody, oczywiście do ocieplania miejsce, które tego wymagają – mówi dyrektor w firmie Arup.
Innowacyjnym rozwiązaniem jest także elektryczny kocioł do produkcji pary, który jest pierwszym takim urządzeniem wprowadzonym na tak dużą skalę w Europie. – W zakładzie funkcjonują dwa kotły do wytwarzania pary – potrzebnej w procesie obróbki kukurydzy – jeden na prąd, drugi na gaz. Stosuje się je zamiennie, w zależności od cen energii. Docelowo ma być używany ten na prąd, gdy zostanie uruchomiona cała produkcja prądu z własnych źródeł OZE – wyjaśnia Associate, Arup.
Ciepło w obiekcie odzyskuje się z każdego możliwego miejsca: ciepło z kominów na piecach technologicznych oraz wymiennikach technologicznych jest podłączony do systemu wody grzewczej, zapewniając ciepło dla budynku, ciepło ze sprężarek powietrza jest wykorzystywane do ogrzewania wody użytkową.
(Wodny) obieg zamknięty
Kolejny istotny element ekologicznego podejścia to zmniejszenie do minimum zużycia wody wodociągowej. – Ważne było także opracowanie obiegu zamkniętego wody. Obiekt został wyposażony we własną oczyszczalnię ścieków. Dużą innowacją było także wykorzystanie wody deszczowej. W fabryce opracowaliśmy system, który zbiera ją, przetrzymuje w zbiorniku retencyjnym, a następnie uzdatnia się ją i używa do chłodzenia – mówi Tomasz Frej z firmy projektowej. Woda deszczowa jest zbierana nie tylko z budynków, ale i z chodników i dróg. Wykorzystuje się ją nie tylko w wieżach chłodniczych, lecz także – po uzdatnieniu – do płukania, mycia i transportu ziemniaków na linie produkcyjne.
Recykling na najwyższym poziomie
Innym elementem gospodarki cyrkularnej, zaprojektowanej przez firmę Arup, jest odzyskiwanie składników produkcji. Stworzono m.in. system odzyskiwania skrobi z wody poprocesowej.
– Docelowo odpadki będą kompostowane również w generatorze biomasy w celu wytworzenia gazu używanego do wytwarzania ciepła na liniach produkcyjnych. Pozostałe odpady organiczne będą suszone i dostarczane jako nawóz tym rolnikom, którzy mają podpisane kontrakty z FritoLay – dodaje Tomasz Frej.